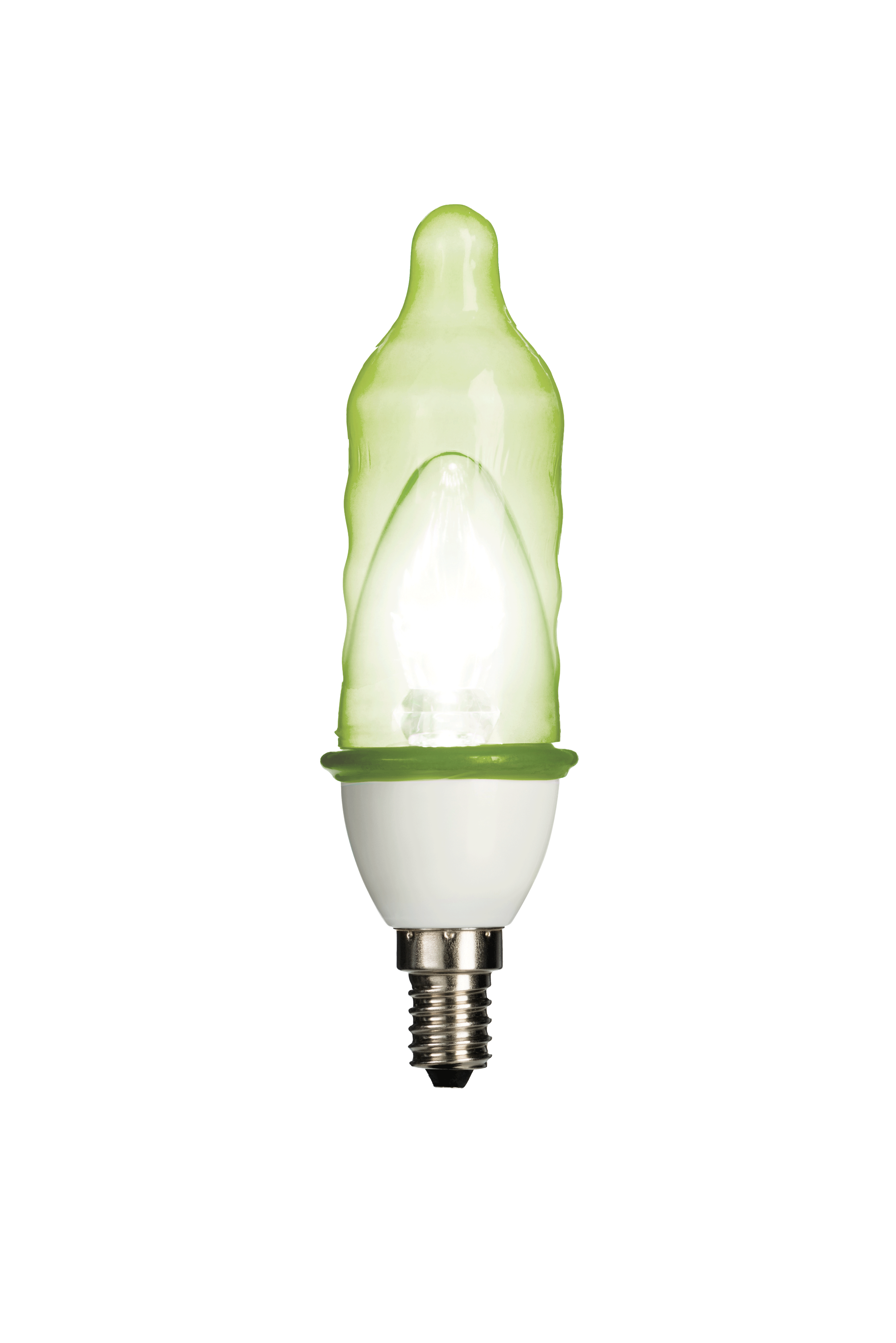
Energy Management and Industry 4.0
automated | seamless | flexible
Energy monitoring as an integrated component of an energy management system or a production according to modern Industry 4.0 standards must, in addition to the most automatic possible generation of key figures, above all master the most complete possible recording of many parameters and be open for everything else that arises in addition to electrical power.- Automatic creation of key figures
- Energy accounting
- Energy accounting
- Interaction with the ERP system
Measuring devices - small and compact
Measuring devices for an energy monitoring system must above all be small, simple and inexpensive and ideally have the following features:- DIN Rail or panel mount
- single-phase or 3~
- Web interface
- Ethernet or serial
- Direct current measurement or sensors (Rogowski coil)
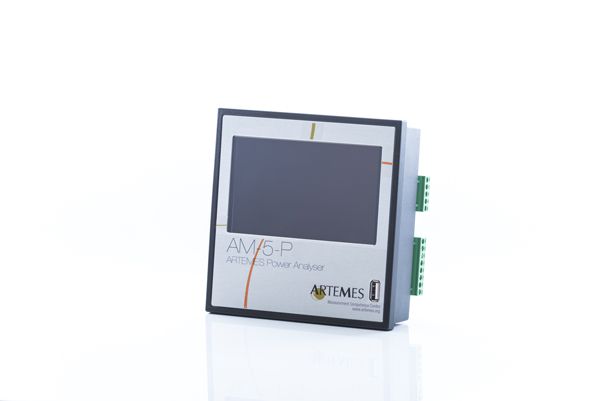
Uninterrupted installation
Especially in the case of plants that are already in operation, people tend to refrain from installing an energy monitoring system because they do not want to accept any interruptions in production. Such interruptions were necessary mainly due to the installation of the current sensors. With the devices of the series
AM-2-R and AM-3-R energy meters WITHOUT such interruptions can be installed without any problems. The Rogowski coils are simply clamped around the busbar.- Installation without interruption of operation
- Immediately ready for operation
- Top-hat rail (DIN) or panel mounting
Disturbances in the power grid - where do they come from?
Unfortunately, disturbances in the electricity grid are often part of it and you often don't know where they come from. In addition to energy meters, grid analysers for fault records and grid quality can help here. These offer fault recording in very high resolution.
- Fault recording in high resolution
- Voltage fluctuations and flicker
- Harmonics
- symmetrical components
- Frequency
- same user interface
You want to record several branches at the same time?
When integrating branches into an energy monitoring system, the data connection is often the limiting factor. The server should be centrally located in the main building and the measuring devices should be integrated via the intranet if possible and via the internet on a case-by-case basis - no problem for the AM-2 data hub.- Intermediate storage of multiple AM-2 or AM-3 load profile data
- Connection to the server according to schedule or constantly
- Use of secure VPN connections
- Intermediate storage in case of data network failure or bottleneck
- Evaluation of data from all branches also possible on site
... and it may also be a little more?
The AM-10-CLOG completes the range and, with its numerous interfaces, offers the possibility of integrating many other data:- Environmental data
- Data from the production
- Data from other measuring devices connected via interfaces
- Small-signal inputs
- RS485 inputs
- Ethernet
- Modbus serial and Ethernet
